Enamel kettle cleaning:
Enamel kettle is a special reactor with a layer of glass enamel inside the metal kettle body. It is widely used in chemical, pharmaceutical, food and other industries. Chemical reactions or material processing are completed by heating, cooling, stirring and other operations of the materials in the kettle. The kettle wall is corrosion-resistant and easy to clean. In order to ensure the life and purity of the reaction, it is recommended to use CYCO automatic cleaning equipment.
Using three-dimensional high-pressure water jet cleaning technology, high-pressure pump is used to pump high-pressure water, which reaches the nozzle through a certain pipeline, and converts high-pressure and low-flow water into high-pressure and high-flow jets. This jet, with its high impact kinetic energy, continuously acts on the surface to be cleaned, causing the scale to fall off and achieve the purpose of cleaning.
Equipment composition:
1. High-pressure pump: provides high-pressure water source and is the core component of the cleaning equipment.
2. PLC intelligent control: one-button start of cleaning operation, control of equipment start, stop, adjustment of cleaning parameters, etc.
3. Automatic telescopic device: vertical automatic lifting and telescoping, fixed-point cleaning. It includes two parts: automatic cleaning device and manual cleaning device. The automatic cleaning device can achieve 360° cleaning of the reactor without dead angles through a three-dimensional automatic rotating nozzle.
4. Three-dimensional rotating cleaning ball: The cleaning nozzle can achieve 360-degree vertical and horizontal three-dimensional rotation and full coverage cleaning, penetrate into the reactor, avoid obstacles, and achieve all-round cleaning.
Cleaning process:
Cleaning equipment in place – the equipment needs to be manually pushed to the side of the reactor, align the manhole, lock the flange, connect water, power on, and ventilate, and confirm that all parts are ready for installation
Start cleaning – After the operator starts the system, it enters the cleaning state, divided into 3 height positions, and symmetrically cleaned at 2 points along the center line of the reactor. The cleaning time of each position can be manually controlled and changed, and the set time needs to be changed in the page of the touch screen.
After cleaning, the disc circler retracts the water pipe in time, disconnects the water, electricity, and gas, and the Panasonic adapter, and then moves to the next tank to be cleaned.
Estimated cleaning time: about 10-20 minutes/tank, according to the customer’s cleanliness requirements.
Industry application:
Mainly used for cleaning inside cubic enamel in industries such as pharmaceuticals, food, beverages, coatings, building materials, chemicals, pigments, resins, scientific research, dairy products, daily chemicals, cosmetics, bioengineering, agricultural engineering, and processing tools, including intelligent automatic cleaning of various stereoscopic kettles such as medium-sized and large reactors, chemical resin acrylic reactors, and stirring kettles.
Cleaning Effect
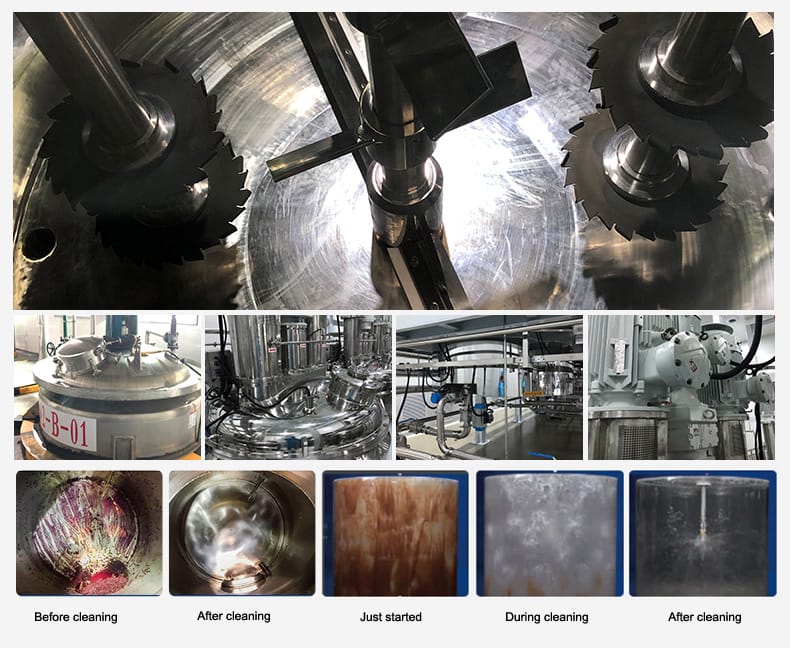